Let’s start with some “before photos” of the layout of the galley and main salon before the “can of worms”. Note the beast of a microwave, trash compactor, the upholstered valances, overhead lights and headliner, speakers, book shelf, desk and double-decker media cabinet. We had six reverse-air units onboard when we purchased Docktails, five stayed aboard until the Pacific Northwest (we ditched the one in the pilothouse in Florida as it was in-operable). The fifth in the galley was removed to make room for Tom’s AV Cabinet.
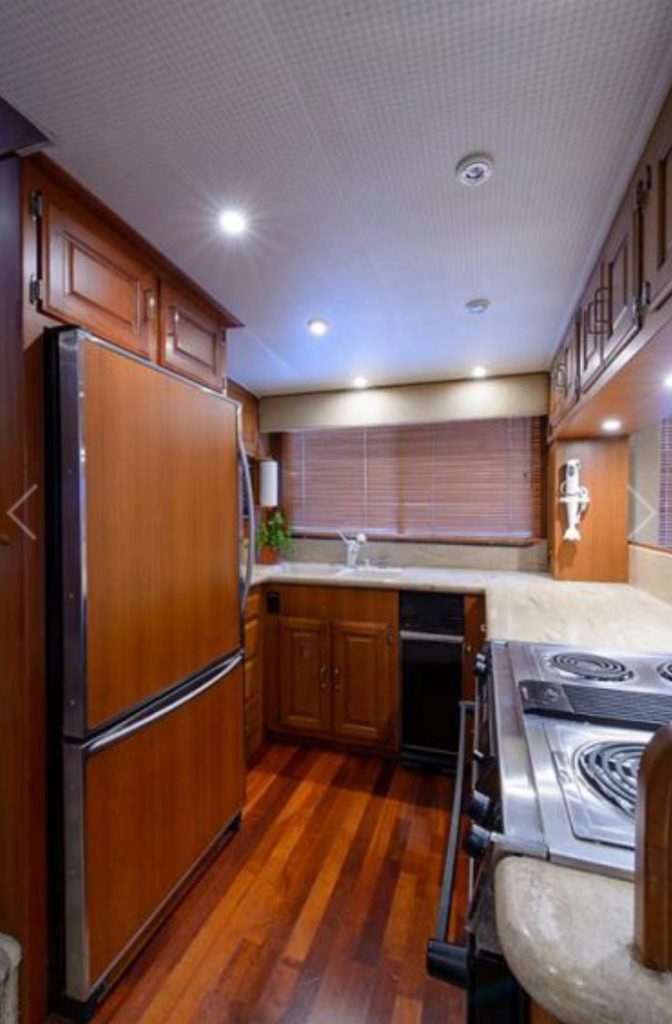
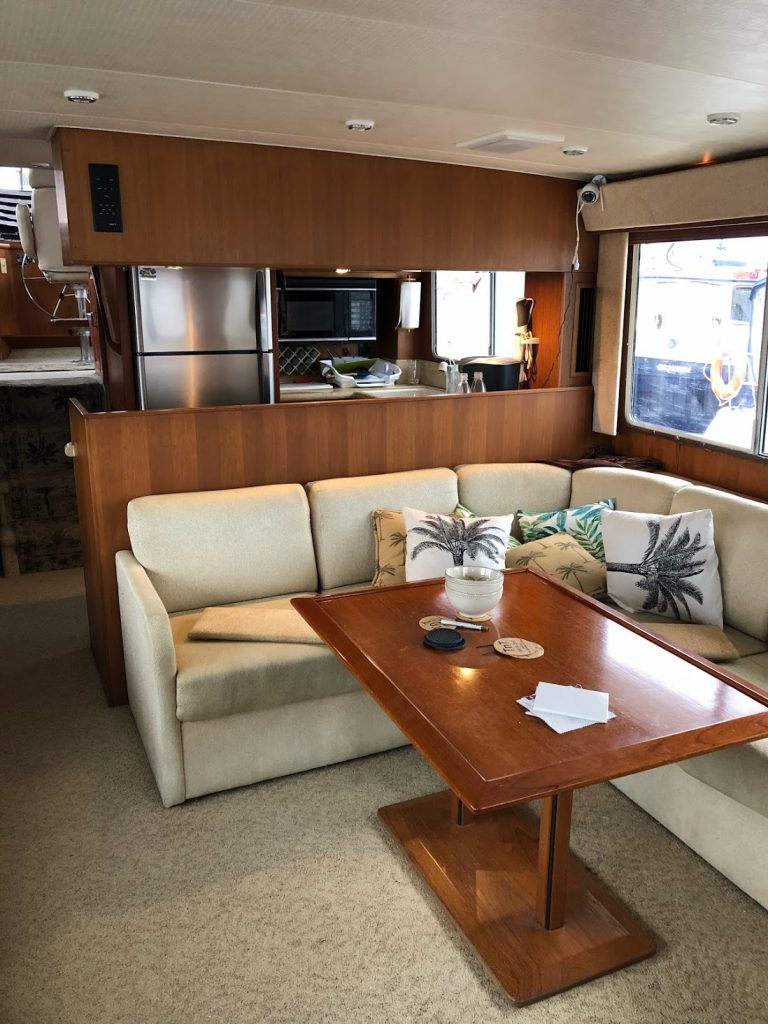
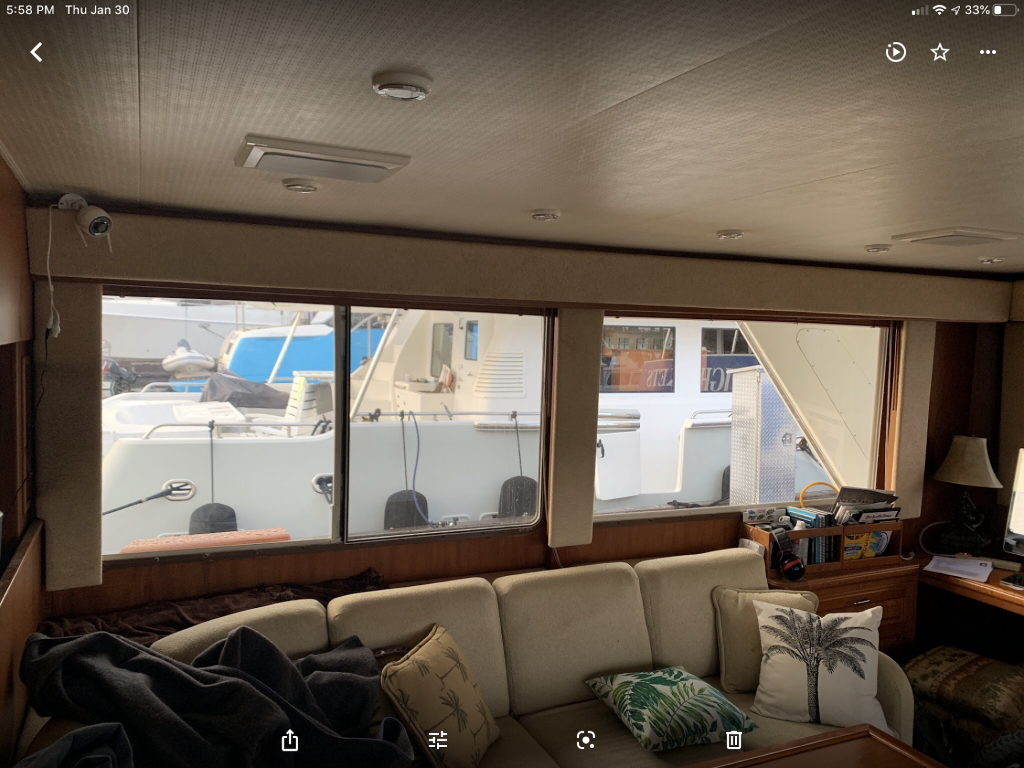
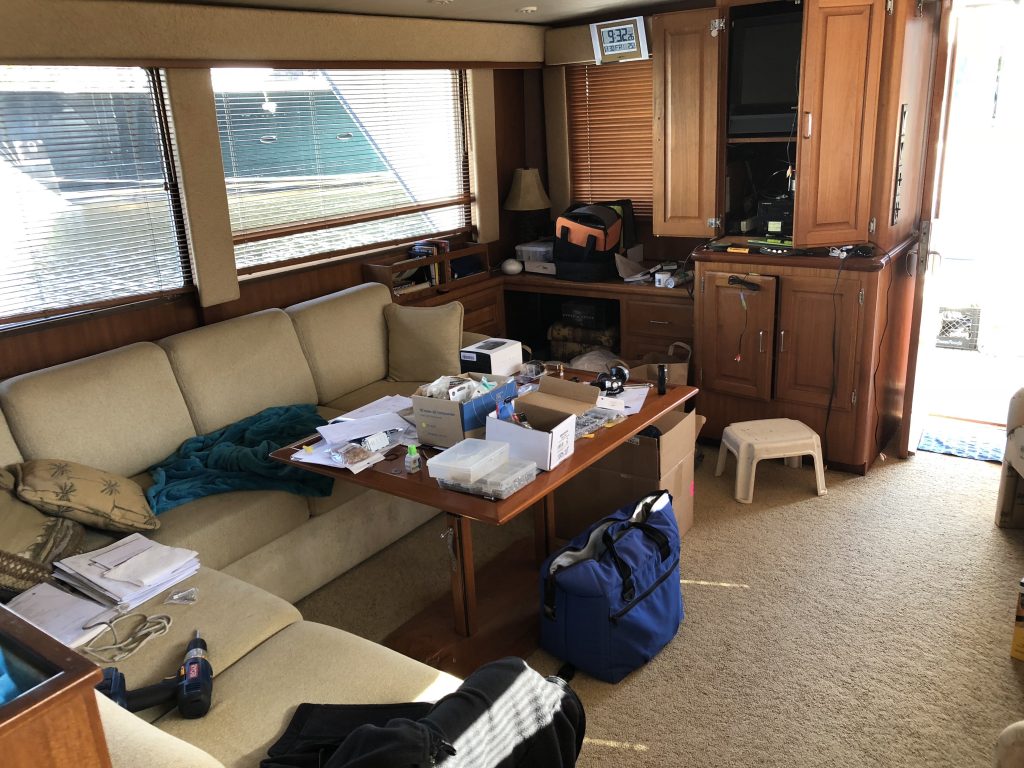
Demo of the galley and main salon was quick work, besides the media cabinet (built like a brick) and the galley sink (equivalent weight of a ton of bricks). As previously mentioned, “Tolly” Tollefson built boats to last.
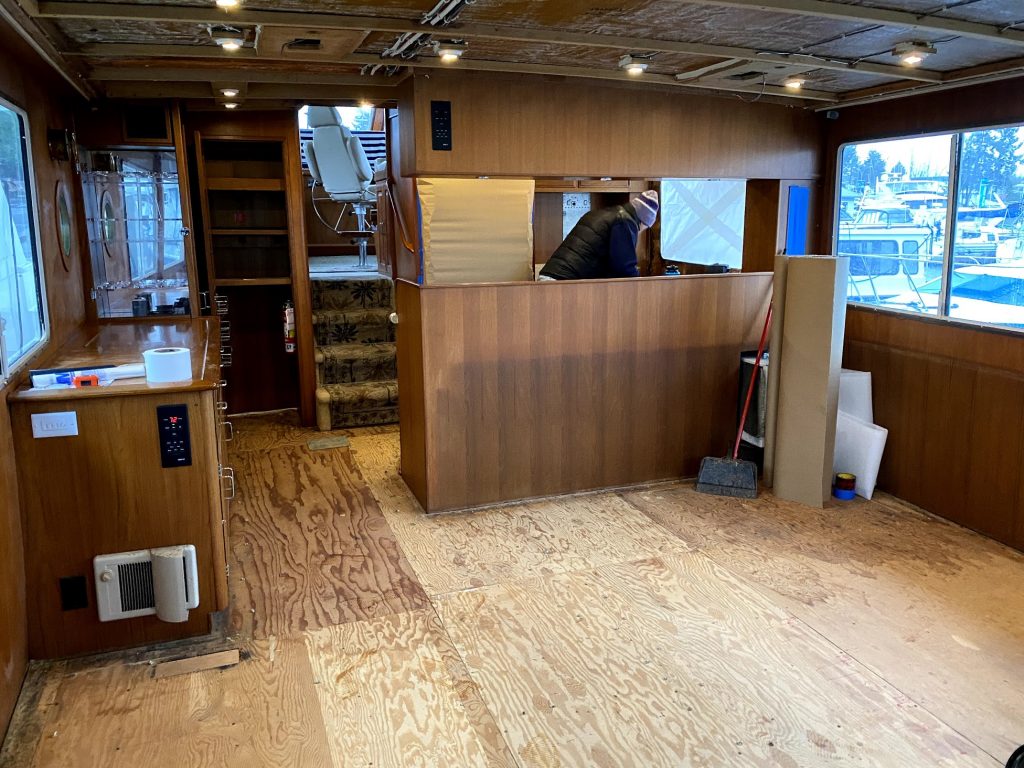
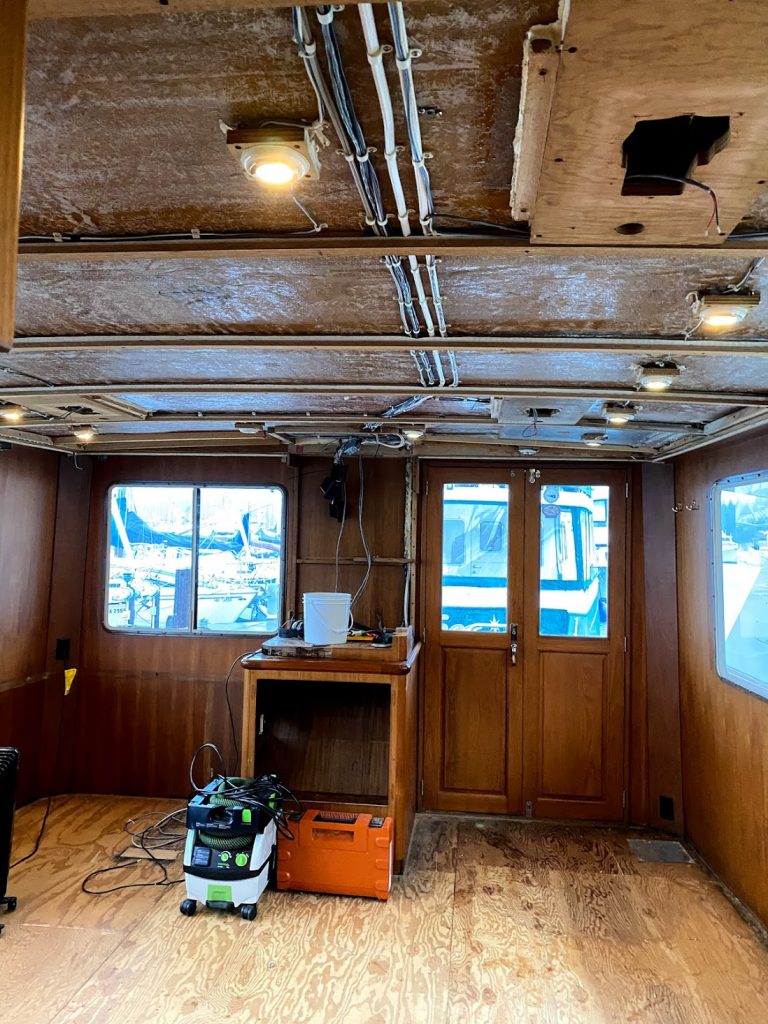
Our “can of worms” was the galley window. We knew it had a leak from above that we had missed on the survey in Ft Lauderdale (those valances hid a lot), but noticed once back in the Pacific Northwest on those days relentless rainy days. The plan was to replace all opening windows with non-opening windows (we only every opened the windows when our A/C was kaput in The Bahamas), fix the galley window leak and damage, keep the cabinets but replace the countertop and the ceramic sink. Our plateware and glassware was dwindling – thanks to this ceramic sink. Tessa was ready to say adieu.
Well, that galley window leak was much more than a small leak. The plywood behind the teak would have to be replaced below the countertop/behind the lower cabinets in addition to above the countertop surrounding the window opening. So, out the lower cabinets came for a complete galley retrofit (cha-ching).
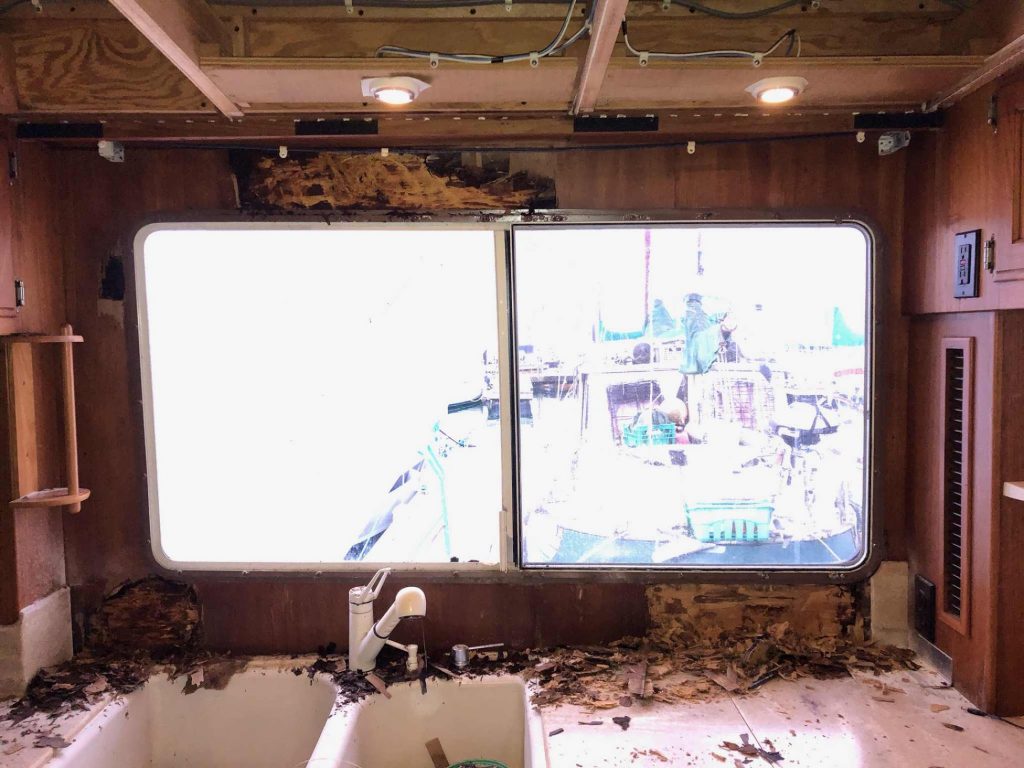
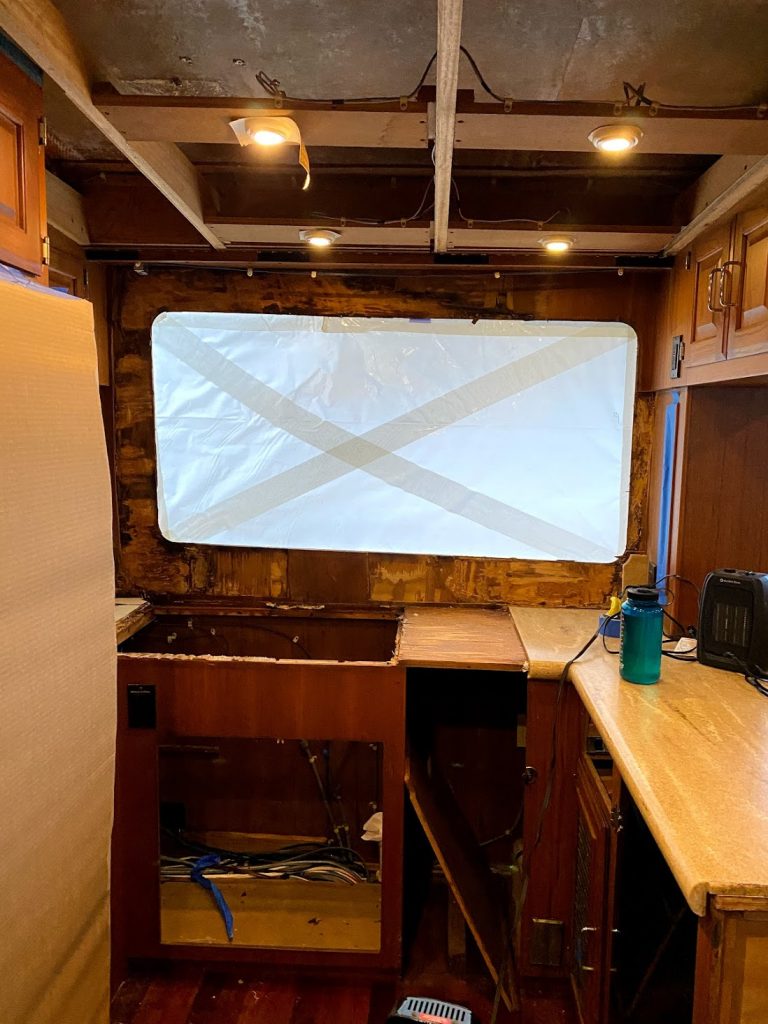
With the headliner removed, they were able to identify that our boat was the equivalent of Swiss cheese. We were far from a water tight boat. All the stainless steel screws had failed in the stanchions on the flybridge (which is the ceiling of the main salon), and there was a 18″x18″ spot in the media cabinet that was pure mud. Needless to say they did a lot of fiberglass patching, and replaced all the stainless steel screws in the stanchions (cha-ching).
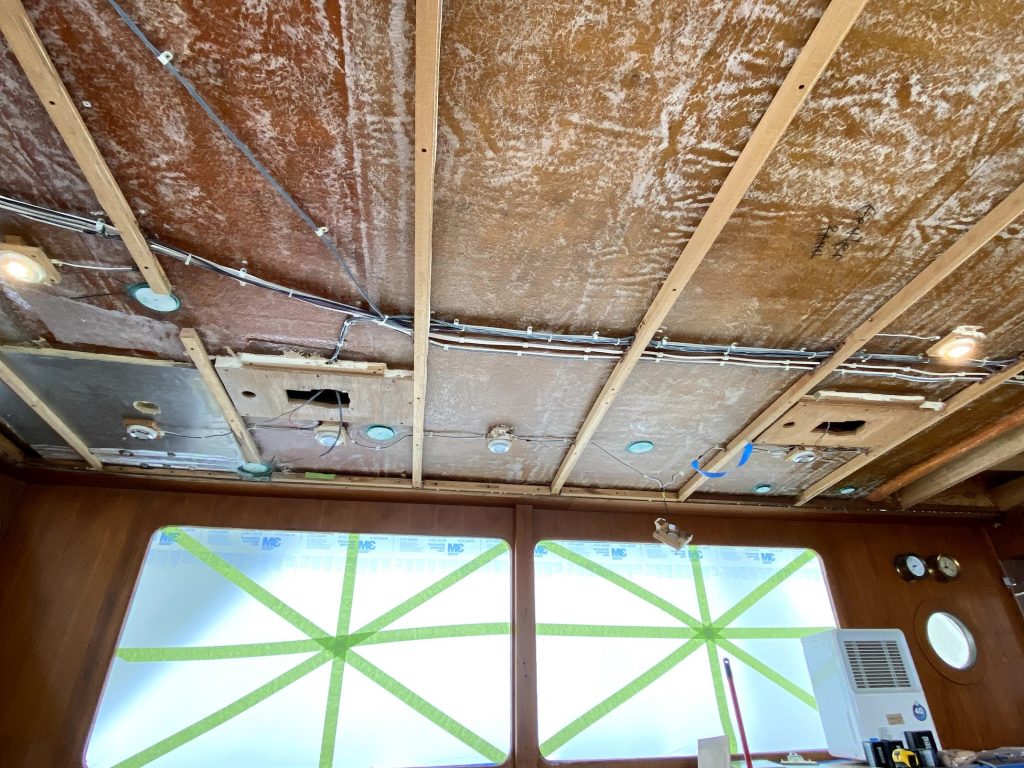
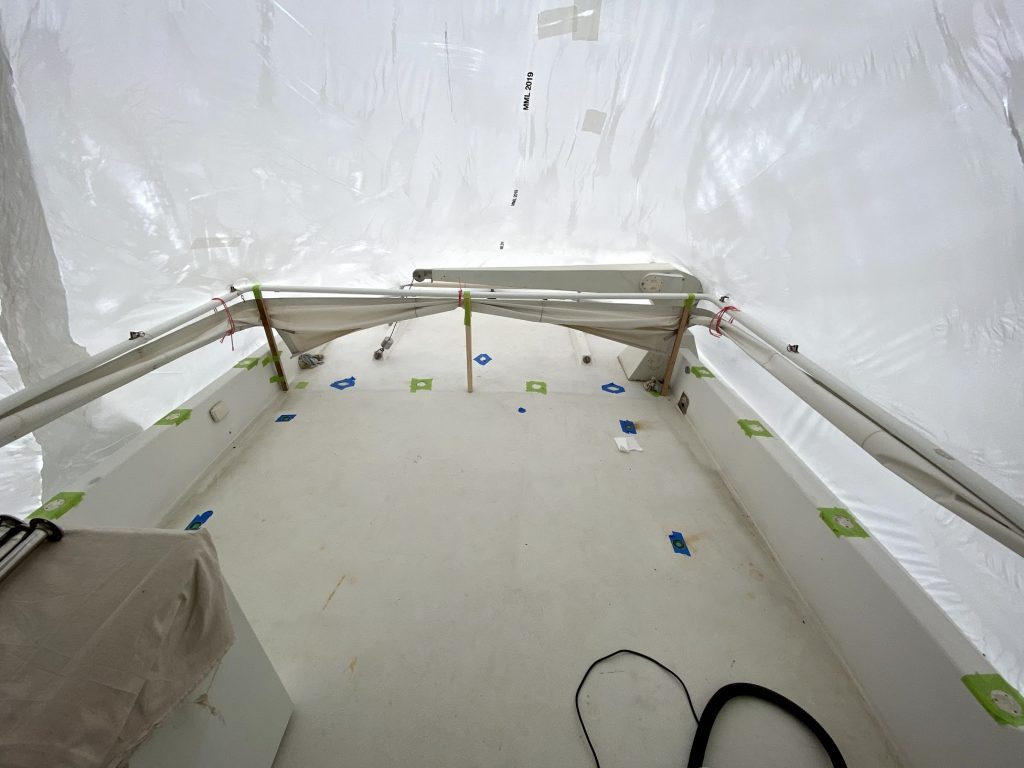
Even though the focus was on the galley and main salon, the Philbrooks Team left no stone unturned. They checked for water leaks from bow to stern, top to bottom. Many of our portholes had failed, and they patched the punky wood around them and rebuilt the portholes. Not surprisingly, the forward stanchion stainless steel screws had also failed. There was an aluminum strip on the radar arch and around the upper helm that had failed – which was the culprit to all the water leaking into our galley window.
As we like to spend most of our time at anchor during the cruising season, Tom asked them to service our windlass. You could say this was our second “can of worms”. Not only was our windlass beyond serviceable, the bow sprit had to be rebuilt, and a 3’x5′ portion of the decking was rotted from the poor installation of the windlass and foot switch controls. Which meant a huge fiberglass decking project (cha-ching). As we have painted teak decking, we either had to replace the decking from bow to stern, or figure out a way to only do a section. Philbrooks did an outstanding job of replacing the fiberglass on the forward quarter of the boat and matching it to the decking on the bump up over the vberth. You’d never know there had been major fiberglass repair work completed.
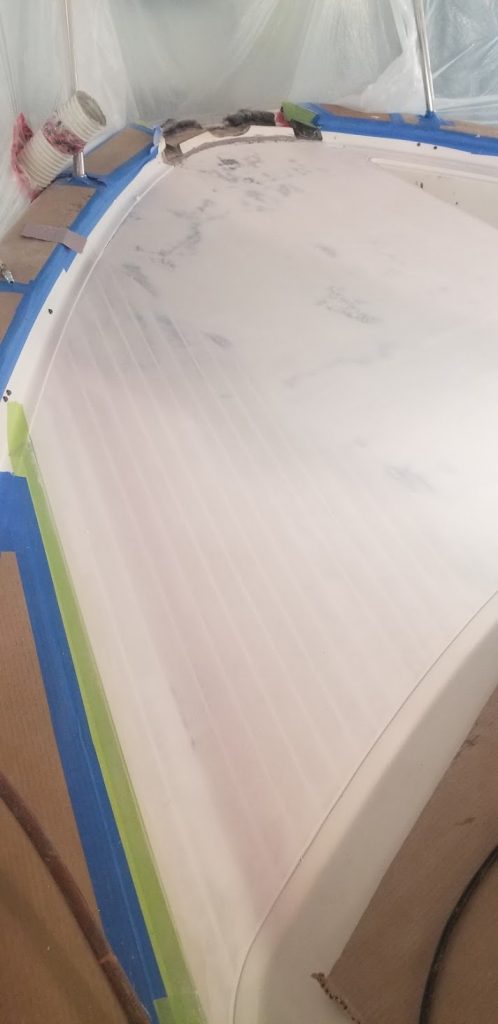
As you know, a pandemic was in its early stages as we began our boat retrofit in January 2020. We were making the trek from Bainbridge Island WA to Sidney BC every ten days or so to check in on the progress and answer any questions the Philbrooks Team had on wiring, placement of hardware, what color carpet/countertop/headliner and wood customizations. We are thankful to have been there in person for some critical decisions on the galley and main salon before the border shut down to non-essential travel mid-March 2020.
We then had to put our trust in the Philbrooks Team to bring to fruition our desires in the retrofit. We adapted to virtual meetings; weekly FaceTimes and even more frequent text conversations with photos. This was easier for us with the galley and main salon, as the critical decision making for these projects were already completed before the border closure.
However for the custom hardtop it required us to have complete faith in the Philbrooks Team on something we did not want to be disappointed with in the final product (cha-ching). FaceTime video included a lot of scaffolding and not great visibility of the hard top. Our Project Manager Jamie allayed our fears and calmed us down on multiple occasions. And nine and a half months later (and more work still to come) when we took possession of her in Roche Harbor mid-September 2020, as the border remained closed, all of our fears were allayed. But more on the custom hard top in another post!